Methode zur Auswahl der besten Bohrer für Ihre Bohrarbeiten
Bei der mechanischen Bearbeitung macht die Bohrarbeitsbearbeitung etwa 1/5 der gesamten Bearbeitungsmenge aus, die Bohrarbeit etwa 30 % der gesamten Lochbearbeitung.Beim Kauf von Bohrern gibt es Bohrer in verschiedenen Farben, Materialien, Handwerken und Handwerken.
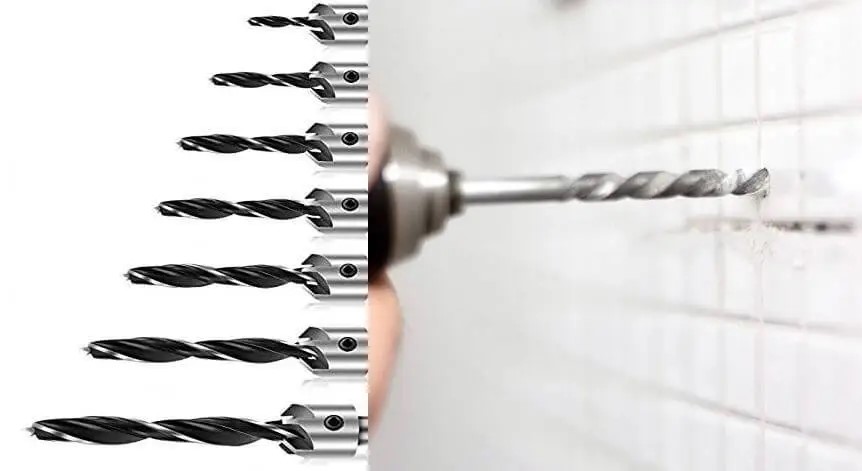
Hier sind zum Beispiel einige Fragen, die Sie möglicherweise stellen müssen, bevor Sie Bohrer kaufen:
Was ist der Unterschied zwischen den Bohrern verschiedener Handwerke?
Was ist der Unterschied zwischen den verschiedenen Farben der Bohrer?
Gibt es einen Zusammenhang zwischen der Farbe und der Qualität des Bohrers?
Welche Bohrerfarbe ist besser?
1, Auswahl der Bohrer entsprechend dem Aussehen der Bohrer, Farbe und Aussehen.
Gibt es beispielsweise einen Zusammenhang zwischen der Farbe des Bohrers und seiner Qualität?Die unterschiedlichen Farben sind vor allem auf unterschiedliche Verarbeitungstechniken zurückzuführen.
Bohrer in der Farbe Weiß:
Hochwertige, vollständig geschliffene Bohrer aus Schnellarbeitsstahl erscheinen häufig in Weiß.Bei gewalzten Bohrern kann durch Feinschleifen des Außenkreises auch Weiß erreicht werden.
Es ist von hoher Qualität, da die Qualitätskontrolle während des Schleifprozesses und des Materials selbst ebenfalls recht streng ist.Es entstehen keine Verbrennungen auf der Oberfläche des Werkzeugs.
Bohrer in der Farbe Schwarz:
Der schwarze Bohrer ist ein Bohrer, der nitriert wurde.Dabei handelt es sich um eine chemische Methode, bei der das fertige Werkzeug in eine Mischung aus Ammoniak und Wasserdampf gegeben und auf 540–560 °C erhitzt wird, um seine Haltbarkeit zu verbessern.(Es gibt auch schwarze Bohrer auf dem Markt, von denen die meisten nur schwarz sind (um die Verbrennung oder schwarze Haut auf der Oberfläche des Werkzeugs abzudecken), aber der tatsächliche Nutzungseffekt wurde nicht effektiv verbessert.)
Bei HEYGO finden Sie schwarze Bohrer;Unsere Bohrer sind tatsächlich nitriert.(Kann ein Video aufnehmen)
Bohrer in Goldfarbe:
Der goldfarbene Bohrer ist mit Titannitrid beschichtet, unterteilt in dekorative Beschichtung und industrielle Beschichtung.Die dekorative Beschichtung stört überhaupt nicht, aber die Farbe ist golden.
Bohrer in der Farbe Hellbraun:
Im Allgemeinen wird diese Farbe durch kobalthaltige Diamanten erzeugt.Ursprünglich weiß, wird es durch Mahlen hergestellt, und wenn es später zerstäubt wird, wird daraus gelblich-braunes M35 (im Allgemeinen Bernstein genannt) (Co 5 %).
2, Auswahl der Bohrer entsprechend dem Material der Bohrer
Die auf dem Markt am häufigsten verwendeten Materialien für Bohrer sind 4241/4341/9341/6542/M35/M42, und ihre Leistung steigt sukzessive.
4241/4341 Material
Dieses Bohrermaterial eignet sich zum Bohren gewöhnlicher Metalle wie Eisen, Kupfer, Aluminiumlegierungen und anderer Metalle mit niedriger und mittlerer Härte sowie Holz, ist jedoch nicht ideal zum Bohren von Metallen mit hoher Härte wie Edelstahl und Kohlenstoffstahl.
Die Qualität ist im Rahmen des Anwendungsbereichs einigermaßen gut, für den Großhandelsverkauf im Baumarkt geeignet.
9341 Material:
Dieses Material eignet sich zum Bohren gewöhnlicher Metalle wie Eisen, Kupfer, Aluminiumlegierungen und anderer Metalle und Holz.Es ist ideal zum Bohren dünner Edelstahlplatten.Dicke Exemplare werden nicht empfohlen.Im Anwendungsbereich ist die Qualität mittelmäßig.
6542 Material:
Dieses Material eignet sich zum Bohren verschiedener Metalle wie Edelstahl, Eisen, Kupfer, Aluminiumlegierungen sowie anderer niedrig- und mittelharter Metalle und Holz.Die Qualität ist im Anwendungsbereich mittel bis hoch und die Haltbarkeit sehr hoch.
Kobalthaltiges Material M35:
Dieses Material ist derzeit die beste Schnellarbeitsstahlsorte auf dem Markt.Der Kobaltgehalt garantiert die Härte und Zähigkeit des Schnellarbeitsstahls.Geeignet zum Bohren verschiedener Metalle wie Edelstahl, Eisen, Kupfer, Aluminiumlegierung, Gusseisen, 45#-Stahl, andere Metalle und verschiedene weiche Materialien wie Holz und Kunststoff.
Die Qualität ist hochwertig und die Haltbarkeit ist besser als bei allen vorherigen Materialien.Wenn Sie sich für den Werkstoff 6542 entscheiden, empfiehlt sich die Wahl von M35.Der Preis ist etwas höher als 6542, aber der absolute Wert.
M42:
Er wird üblicherweise als Bohrer mit hohem Kobaltgehalt bezeichnet, da sein Kobaltgehalt 8 % erreicht.Im Allgemeinen beträgt der dem Schnellarbeitsstahl-Rohstoff zugesetzte Kobaltgehalt bis zu 8 %, und mehr wird zu Hartmetall.Der Zweck der Zugabe von Kobalt besteht darin, die Hochtemperaturbeständigkeit und die Abriebfestigkeit des Bohrers zu verbessern.
3, Auswahl der Bohrer entsprechend den Herstellungsprozessen der Bohrer
Zur Herstellung von Bohrern gibt es drei Verfahren: Walzen, Fräsen und Schleifen.
Die zentralen Bearbeitungstechniken von Spiralbohrern sind die Spiralnutbearbeitung, die Wärmebehandlung und das Schärfen.Da die Wärmebehandlung und die anschließenden Schleifprozesse gleich sind, liegt der Hauptunterschied in der Formung des Arbeitsteils des Spiralbohrers.
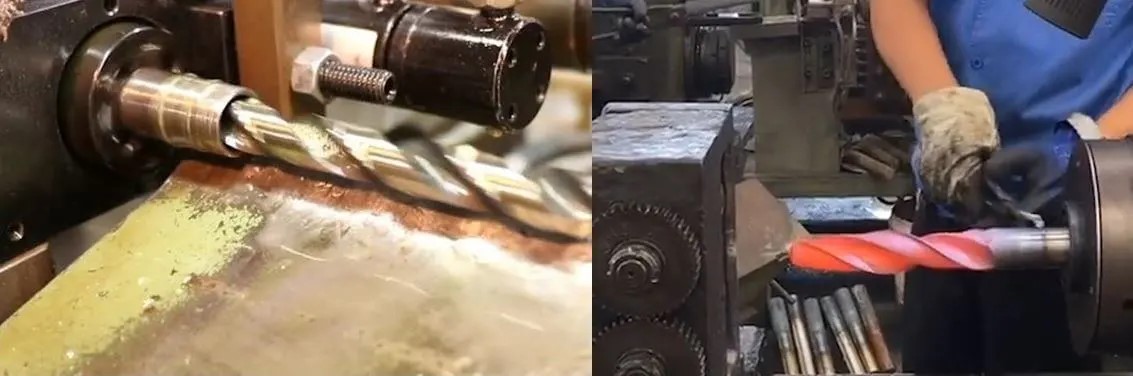
Derzeit wird es zur Herstellung von Spiralbohrern verwendet.Beim Umformprozess des Bohrteils gibt es hauptsächlich drei Methoden: Fräsverfahren, Walzverfahren und Schleifverfahren.
Fräsmethode für Bohrer:
Mit einem Formfräser die gewünschte Spiralnutform auf den ungehärteten Spiralbohrerrohling fräsen.Das Fräsverfahren verfügt über ein umfangreiches Bearbeitungsspektrum und verarbeitet hauptsächlich Spiralbohrer von 10 bis 70 mm.
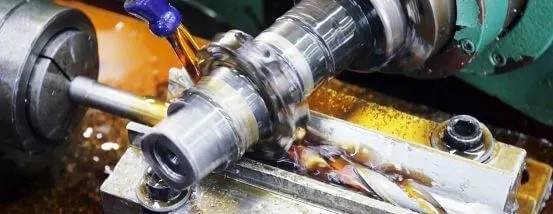
Fräsmethode Der Nachteil besteht darin, dass die Werkzeugkosten hoch sind, die Bearbeitungszeit lang ist und die endgültige Form vor der Wärmebehandlung bearbeitet wird.Der beim Härten entstehende Geometriefehler spiegelt sich nahezu vollständig im fertigen Bohrer wider.
Rollen für Bohrer:
Rollen Sie vier fächerförmige Platten auf dem erhitzten Rohling, um die Form des Bohrers zu erhalten.Im Vergleich zur Fräsmethode weist der durch plastische Verformung hergestellte Bohrer eine geringere Genauigkeit auf.
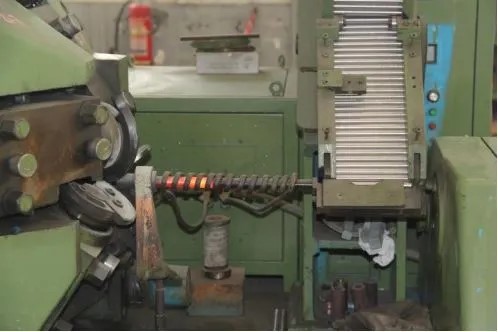
Aufgrund des geometrischen Fehlers, der durch die Verformung des gewalzten Spiralbohrers durch die Wärmebehandlung verursacht wird, kann er außerdem die Anforderungen zum Bohren hochwertiger Löcher nicht erfüllen.Der Vorteil dieser Methode besteht vor allem darin, dass Rohstoffe für die Herstellung von Spiralbohrern eingespart werden, sodass die Wirtschaftlichkeit gut ist.Der maximale Durchmesser des Vierwalzenwalzverfahrens beträgt 40 mm.
Schleifen für Bohrer:
Wenn die Geschwindigkeit der Schleifscheibe 100 m/s erreicht, ist es mit der neuesten Version möglich, die Spiralnut des Spiralbohrers aus dem gesamten Material zu schleifen.Hochgeschwindigkeitsschleifen kann die Schnittkraft reduzieren, die Oberflächenqualität deutlich verbessern und Formfehler reduzieren.
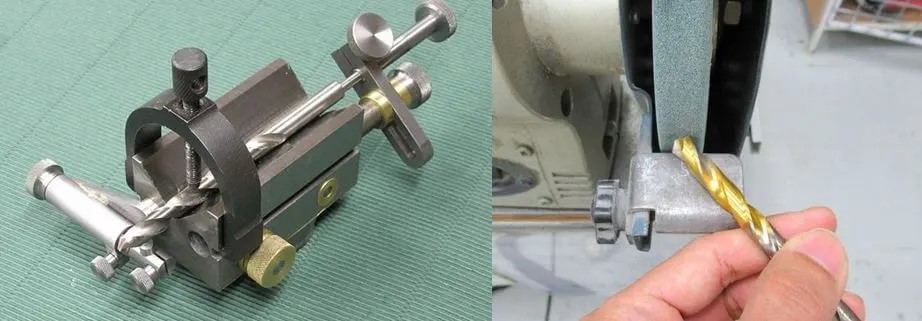
Im Vergleich zur Fräsmethode kann die Schleifmethode die Einzelarbeitsstunden erheblich reduzieren und die Qualität ist hoch und stabil.Derzeit können mit dem Schleifverfahren nur Spiralbohrer mit einem Durchmesser kleiner l5 hergestellt werden.
Was sind ihre Unterschiede und Eigenschaften?
Technische Analyse und wirtschaftliche Auswirkungen von drei Verarbeitungstechniken:
1. Technische Indikatoren
|
| Mahlen | Rollen | Schleifen |
Rauheit Ra (μm) | Innovativ, auf dem neuesten Stand | 4.6 | 6.5 | 2.5 |
Klingennut | 8.6 | 12.5 | 3.2 | |
Die Symmetrie der Klinge |
| 0,105 | 0,301 | 0,03 |
Radialschlag |
| 0,05 | 0,08 | 0,03 |
Normaler Sprung |
| 0,05 | 0,18 | 0,03 |
2.Verarbeitungseffizienz
Da die Verarbeitungstechnologie von Spiralbohrern bis auf Spiralnuten dieselbe ist, sind auch die übrigen Verarbeitungsverfahren gleich.Aus diesem Grund wird nur die Bearbeitungszeit ihrer Spiralnuten verglichen.Einige Beispiele für die Bearbeitung von 12-mm-Spiralbohrern mit Zylinderschaft in einer Stunde.
Prozesse | Mahlen | Rollen | Schleifen |
Verarbeitungseffizienz | 18 | 250 | 98 |
3. Der geschliffene Spiralbohrer weist eine hohe Maßgenauigkeit und eine gleichmäßige Abschreckhärte auf.Die Biegeverformung ist gering und der Spiralbohrer wurde während der Verarbeitung einer Druckbeanspruchung ausgesetzt.
Bei der fräsenden Bearbeitungsmethode wird der Spiralbohrer rollend auf Zug beansprucht.Bei den Walz- und Strangpressverfahren ist die Temperatur schwer zu kontrollieren, + Schnellarbeitsstahlmaterialien neigen zu Entkohlung, Rissen usw., was sich auf die Lebensdauer des Spiralbohrers auswirkt.
Später beträgt der Verschleißwert der Klingenoberfläche VB--0,15 mm als Beispiel, der Verschleißtest des L2-Spiralbohrers mit geradem Schaft unter den gleichen Bedingungen wie der Spiralbohrer.
Prozesse Fräsen Walzen Schleifen
Anzahl der Löcher 28 25 34
Experimentelle Bedingungen:
(1) Verarbeitungsmaterial: vergüteter Austernstahl, HB-190-200
(2) Bohrparameter;V=30m/Regen, f-0,28mm/r, Loch 36mm tief, kein Durchgangsloch.
(3) Schneidflüssigkeit: wässrige Lösung aus emulgiertem Öl
4. Wirtschaftlicher Effekt
Fräsmethode
Die Produktionseffizienz dieser Verarbeitungsmethode ist relativ gering.Es ist nur für die Einzelstück-Kleinserienfertigung geeignet.Der Fräser hat eine komplexe Struktur, einen hohen Preis und viele Verfahren.
Rollen
Die Materialausnutzung ist etwa 25 % höher als beim Fräsen;die Produktionseffizienz ist mehr als zehnmal höher als beim Mahlen;es ist für die Massenproduktion geeignet.
Allerdings ist die Produktionsumgebung dieser Art von Methode weniger sicher;Wenn sich Spezifikationen ändern, ist es schwierig, den Prozess anzupassen.Jeder Prozess Der Parameterwiderspruch ist ausgeprägt und die Ablehnungsrate ist hoch.
Mahlen
Die Produktionseffizienz ist höher als die des Mahlverfahrens;die Biegeverformung wird eliminiert.Der Richtvorgang wird eingespart;Die Verarbeitungsgenauigkeit ist hoch und die Qualität stabil.Die Quote an Verschwendung und fehlerhaften Produkten ist gering.
Der Ausstattungspreis ist hoch.Der Verarbeitungsbereich ist klein und es ist schwierig, Späne hinzuzufügen.
Basierend auf den oben genannten Daten wird daher der Hochgeschwindigkeitsstahl-Schleifbohrer in folgenden Punkten mit dem Walz- und Fräsprozess verglichen:
1,Die geometrische Präzision des Bodenbohrers ist hoch.Unter Verwendung der Walz- und Tonherstellungstechnologie muss die Nutbearbeitung des Bohrers vor dem Abschrecken abgeschlossen sein.Die geometrische Genauigkeit des Bohrers wird aufgrund der Verformung durch die Abschreckbehandlung verringert.
Beim Schleifprozess werden die Nuten nach dem Abschrecken geschliffen, wodurch die durch die Abschreckbehandlung verursachte Verformung beseitigt und die geometrische Genauigkeit des Bohrers verbessert wird.Dadurch kann der Bohrer feiner in Spezifikationen und Größen unterteilt werden, um der präzisen Verarbeitung verschiedener Größen gerecht zu werden.
Die Verbesserung der Glätte des Bohrers verbessert nur die Öffnung und Glätte der bearbeiteten Teile.
2, Lange Lebensdauer von Erdbohrern.Die Praxis hat gezeigt, dass die Lebensdauer des Erdbohrers ein bis zwei Mal länger ist als die des Roll- und Baht-Bohrers.Dies hängt mit der hervorragenden Präzision des geschliffenen Bohrers, der hohen Helligkeit und der scharfen Schneidkante zusammen.
3, Hohe Produktionseffizienz.Mittlerweile hat sich der Schleifprozess zum Hochleistungsschleifen entwickelt und die Produktionseffizienz bei der Bearbeitung von Bohrern hat das Zwei- bis Fünffache der Produktionseffizienz beim Fräsen erreicht.
Allgemein gesagt:
In Bezug auf Genauigkeit/Endbearbeitung/Kosten nehmen alle drei Prozesse zu.Walzen<Fräsen<Schleifen
Egal, ob es sich um einen Endverbraucher, einen Händler oder einen großen Markenkunden handelt, wir können bei der Auswahl des geeigneten Bohrbodens und Lieferanten auch die folgenden Punkte berücksichtigen.
Ob es sich um eine bekannte Marke handelt
Qualität der Vorlieferanten
Bauzeit
Wärmebehandlung
Bearbeitung
Bewusstsein für Qualitätskontrolle
Erkennungsbewusstsein
Mehrchargentests zur Überprüfung der Stabilität