穴あけ作業に最適なドリルビットの選択方法
機械加工では、穴あけ加工が全体の加工量の約1/5、穴あけ加工が全体の穴加工の約30%を占めています。ドリルビットを購入する場合、さまざまな色、素材、工芸品、工芸品のドリルビットがあります。
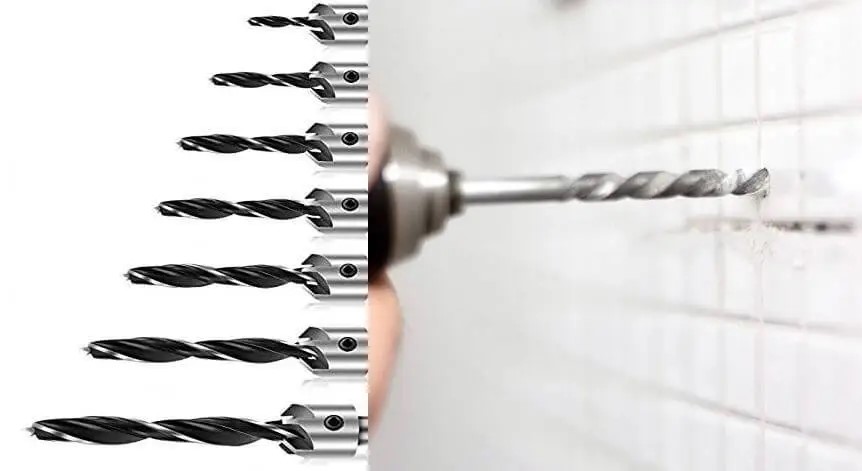
たとえば、ドリルビットを購入する前に尋ねる必要がある質問がいくつかあります。
さまざまな工芸品のドリルの違いは何ですか?
ドリルビットの色の違いは何ですか?
ドリルビットの色と品質には関係がありますか?
どの色のドリルビットが良いですか?
1、ドリルビットの外観に応じてドリルビットを選択します 色と外観。
たとえば、ドリルビットの色とその品質の間には関係がありますか?色の違いは主に加工技術の違いによるものです。
白色のドリルビット:
完全に研削された高品質の高速度鋼ドリルビットは、多くの場合白色で表示されます。転造ドリルビットは、外側の円を細かく研磨することで白色にすることもできます。
素材そのものの研磨工程における品質管理も非常に厳しいため、高品質です。工具の表面に焼けがつきません.
黒色のドリルビット:
黒いドリルは窒化処理が施されたドリルビットです。完成した工具をアンモニアと水蒸気の混合物の中に入れ、540〜560℃で加熱して耐久性を向上させる化学的方法です。(黒色のドリルビットも市販されていますが、そのほとんどは(工具表面の焼けや黒皮を隠すため)ただ黒いだけですが、実際の使用効果は効果的に改善されていません)。
黒色のドリルビットは HEYGO から入手できます。当社のドリルビットは実際に窒化されています。(動画撮影可能)
ゴールドカラーのドリルビット:
ゴールドカラーのドリルビットは窒化チタンでメッキされており、装飾メッキと工業メッキに分けられます。装飾メッキは全く影響ありませんが、色が金色になっております。
黄褐色のドリルビット:
一般に、コバルトを含むダイヤモンドはこの色になります。元々は白色で、粉砕により生成され、後期に微粒子化されると黄褐色(一般に琥珀と呼ばれる)となるM35(Co 5%)。
2、ドリルビットの材質に応じたドリルビットの選択
ドリルビットに使用される市場の一般的な材質は 4241/4341/9341/6542/M35/M42 であり、その性能は順次増加します。
4241/4341 材質
このドリルビットの材質は、鉄、銅、アルミニウム合金などの中低硬度金属や木材などの一般金属の穴あけに適していますが、ステンレス鋼や炭素鋼などの高硬度金属の穴あけには適していません。
品質は用途の範囲内でかなり良好で、ホームセンターでの卸売販売に適しています。
9341 素材:
鉄、銅、アルミ合金などの一般金属や木材の穴あけに適しています。薄いステンレス板の穴あけに最適です。厚いものはお勧めしません。アプリケーションの範囲内では、品質は中程度です。
6542 素材:
ステンレス鋼、鉄、銅、アルミ合金等の低・中硬金属、木材等の各種金属の穴あけに適しています。品質は用途の範囲内では中程度から高で、耐久性は非常に高いです。
M35 コバルト含有材料:
この材料は現在市場で最高グレードの高速度鋼です。コバルト含有により、高速度鋼の硬度と靭性が保証されます。ステンレス鋼、鉄、銅、アルミニウム合金、鋳鉄、45#鋼、その他の金属、木材やプラスチックなどのさまざまな軟質材料などのさまざまな金属の穴あけに適しています。
品質は高級感があり、これまでのどの素材よりも耐久性に優れています。6542 材質を使用する場合は、M35 を選択することをお勧めします。価格は6542より少し高いですが、絶対的な価値があります。
M42:
コバルト含有量が8%に達するため、通常高コバルトドリルと呼ばれます。一般にハイス原料に添加されるコバルトの含有量は8%までであり、それ以上になると超硬合金となります。コバルトを添加する目的は、ドリルの耐高温性と耐摩耗性を向上させることです。
3、ドリルビットの製造プロセスに応じたドリルビットの選択
ドリルビットの製造には、転造、フライス加工、研削という 3 つのプロセスがあります。
ツイストドリルの中心となる加工技術はスパイラル溝加工、熱処理、目立てです。熱処理とその後の研削プロセスは同じであるため、主な違いはツイストドリルの作動部分の形成にあります。
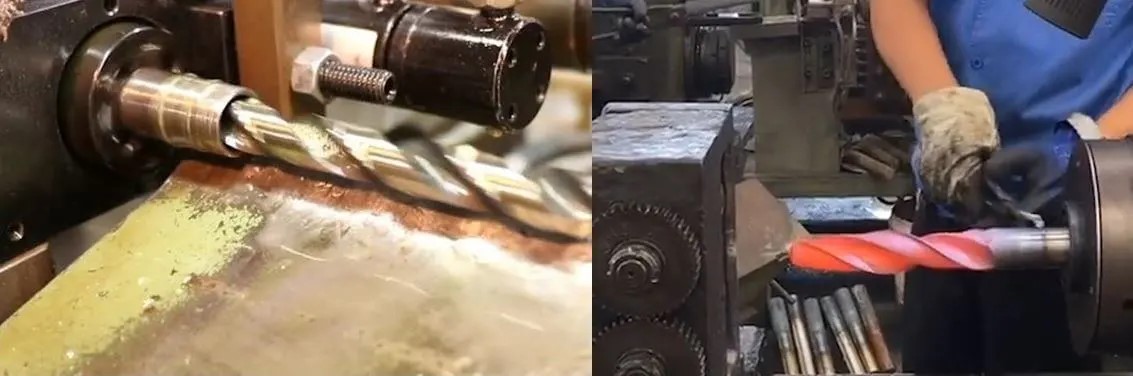
現在、ツイストドリルビットの製造に使用されています。穴あけ部の成形加工には、主にフライス加工、転造加工、研削加工の3つの方法があります。
ドリルビットのフライス加工方法:
フォーミングフライスカッターを使用して、硬化していないツイストドリルブランクに必要なスパイラル溝の形状をフライス加工します。ミーリング工法は加工範囲が広く、主に10~70mmのツイストドリルの加工が可能です。
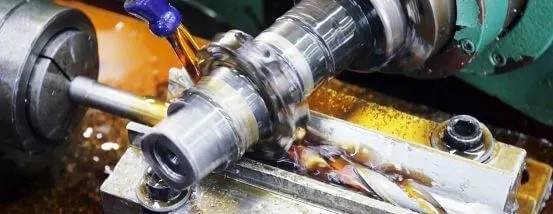
フライス加工法 欠点は、工具のコストが高く、加工時間が長く、熱処理前に最終形状を加工することです。焼入れ中に発生する幾何学的誤差は、完成したドリルにほぼすべて反映されます。
ドリルビットの転造:
加熱したブランクの上で4枚の扇形のプレートを転がしてドリルビットの形状を形成します。塑性変形により製造されるドリルはフライス法に比べて精度が劣ります。
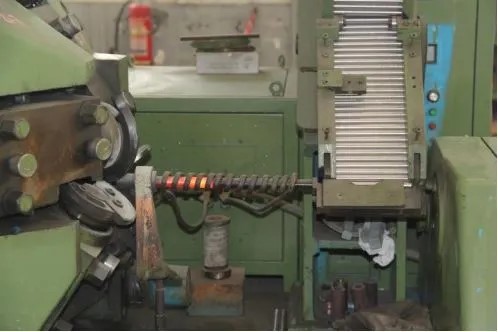
さらに、転造ツイストドリルの熱処理変形によって生じる幾何学的誤差により、高品質の穴加工の要件を満たすことができません。この方法の利点は主に、ツイストドリルを製造するための原材料を節約できるため、経済性が良いことです。4本ロール圧延法の最大径は40mm.
ドリルビットの研削:
最新のものでは砥石の回転速度が100m/sに達すると、ツイストドリルのスパイラル溝を素材全体から研削することが可能になります。高速研削により切削抵抗が低減され、面品位が大幅に向上し、形状誤差が減少します。
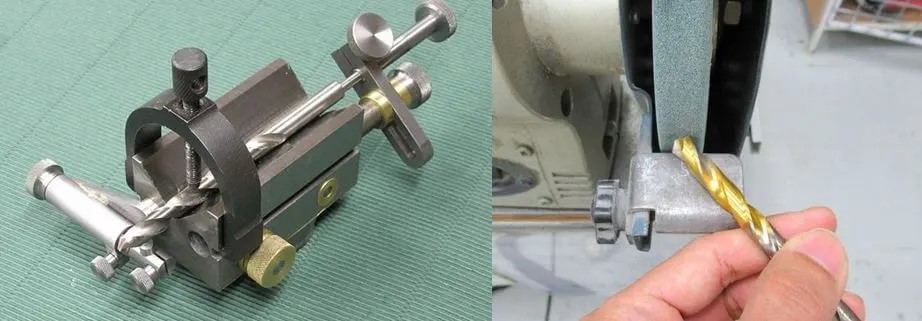
研削法はフライス法に比べて一枚あたりの作業時間を大幅に短縮でき、品質が高く安定しています。現在、この研削方法では直径 15 未満のツイストドリルしか製造できません。
それぞれの違いや特徴は何でしょうか?
3 つの加工技術の技術分析と経済効果:
1. テクニカル指標
|
| フライス加工 | 圧延 | 研削 |
粗さRa(μm) | 最先端 | 4.6 | 6.5 | 2.5 |
刃溝 | 8.6 | 12.5 | 3.2 | |
刃の対称性 |
| 0.105 | 0.301 | 0.03 |
ラジアル振れ |
| 0.05 | 0.08 | 0.03 |
通常ジャンプ |
| 0.05 | 0.18 | 0.03 |
2.処理効率
ツイストドリルはスパイラル溝以外の加工技術は同じですので、その他の加工手順は同様です。このため、スパイラル溝の加工時間のみを比較する。12mm ストレートシャンクツイストドリルを 1 時間で加工した例をいくつか紹介します。
プロセス | フライス加工 | 圧延 | 研削 |
処理効率 | 18 | 250 | 98 |
3. 研削ツイストドリルは寸法精度が高く、焼入れ硬さが均一です。曲げ変形が小さく、加工時に圧縮応力がかかるツイストドリルです。
ミーリング加工では、ツイストドリルに引張応力を加えて転がします。転造加工や押出加工では温度管理が難しく、高速度鋼材は脱炭や割れなどが発生しやすく、ツイストドリルの寿命に影響を与えます。
その後、ツイストドリルと同条件でl2ストレートシャンクツイストドリルの摩耗試験を行った結果、刃面の摩耗値はVB--0.15mmとなっています。
加工 フライス加工 圧延 研削
穴数 28 25 34
実験条件:
(1) 加工材質:オイスター鋼焼入焼戻し品、HB-l90-200
(2) 掘削パラメータ。V=30m/雨、f-0.28mm/r、穴深さ36mm、貫通穴なし。
(3) 切削液:乳化油水溶液
4. 経済効果
フライス加工方法
この加工方法は生産効率が比較的低いです。単一品の小ロット生産にのみ適しています。フライスは構造が複雑で価格も高く、手順も多い。
圧延
材料利用率はフライス加工よりも約 25 高くなります。生産効率はフライス加工の10倍以上です。大量生産に適しています。
ただし、このタイプのメソッドの実稼働環境は安全性が低くなります。仕様を変更する場合、工程の調整が難しい。各工程でパラメータの矛盾が目立ち、不合格率が高い。
グラインド
粉砕法に比べて生産効率が高いため、曲げ変形が解消されます。矯正プロセスは保存されます。加工精度が高く、品質が安定しています。廃棄品や不良品の発生率は低いです。
設備価格が高い。加工範囲が狭く、切りくずの追加が困難です。
したがって、上記のデータに基づいて、ハイス研削ドリルビットと転造およびフライス加工プロセスを次の点で比較します。
1,グランドドリルの幾何精度が高い。転造・トンメイキング技術により、ドリルビットの溝加工は焼入れ前に完了する必要があります。焼入れ処理による変形によりドリルビットの幾何精度が低下します。
研削加工は、焼入れ後に溝を研削することで、焼入れ処理による変形をなくし、ドリルビットの幾何精度を向上させます。これにより、ドリルビットの仕様やサイズをより細かく分けることができ、さまざまなサイズの精密な加工に対応できます。
ドリルビットの平滑性の向上は、加工部品の開口部と平滑性を向上させるだけです。
2, グランドドリルの長寿命。実践により、研削ドリルビットの耐用年数は、ローリングドリルビットやバーツドリルビットの耐用年数よりも1〜2倍長いことが証明されました。これは、研削ドリルビットの優れた精度、高輝度、鋭い刃先に関係しています。
3, 高い生産効率。現在では研削加工は強力研削の段階にまで発展し、マシニングドリルの生産効率はミーリングの2~5倍に達しています。
一般的に言えば:
精度・仕上がり・コストの3つの工程はいずれも向上しています。圧延<フライス<研削
エンドユーザー、流通業者、大手ブランド顧客のいずれであっても、適切な掘削土とサプライヤーを選択する際には、次の点も考慮できます。
有名ブランドかどうか
上流サプライヤーの品質
構築時間
熱処理
機械加工
品質管理に対する意識
検出の認識
安定性を検証するためのマルチバッチテスト