HSS TWIST DRILL BITS
It is the most widely used hole machining tool. Usually, the diameter ranges from 0.25 to 80 mm. It is mainly composed of the working part of the drill bit and the handle. The working part has two spiral grooves, shaped like twists, hence the name. In order to reduce the friction between the guide part and the hole wall during drilling, the diameter of the twist drill gradually decreases from the drill tip to the handle inverted cone. The spiral angle of the twist drill mainly affects the size of the upper front angle of the cutting edge, the strength of the blade and chip removal performance, usually from 25° to 32°. Spiral grooves can be processed by milling, grinding, hot rolling or hot extrusion, and the front end of the drill bit is grinded to form a cutting part. The top angle of the cutting part of the standard twist drill is 118, the bevel angle of the cross edge is 40° to 60°, and the back angle is 8° to 20°. Due to structural reasons, the front angle is large at the outer edge and gradually decreases in the middle. The horizontal edge is a negative front angle (up to about -55°), which plays an extrusion during drilling.
WOOD FLAT DRILL BITS
The cutting part of the flat drill is shovel-shaped, the structure is simple, the manufacturing cost is low, and the cutting fluid can be easily introduced into the hole, but the cutting and chip removal performance is poor. There are two types of flat drills: integral and assembly. The integral formula is mainly used to drill micropores with a diameter of 0.03 to 0.5 mm. The assembled flat drill blade can be replaced and can be cooled internally. It is mainly used for drilling holes with a diameter of 25 to 500 mm.
DEEP HOLE DRILLING
Deep hole drilling usually refers to a tool that processes holes with a ratio of hole depth to aperture greater than 6. Commonly used are gun drills, BTA deep hole drills, jet drills, DF deep hole drills, etc. Sleeve drills are also often used in deep hole machining.
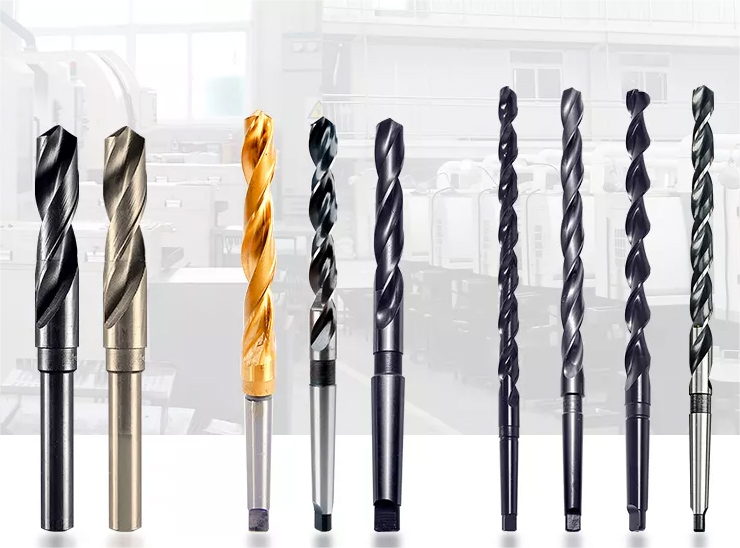
Post time: Apr-11-2023